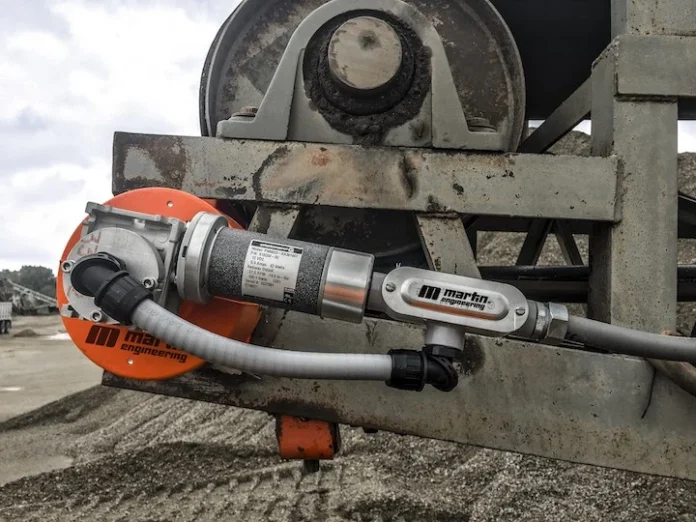
Geri taşınan malzeme, konveyör banttan boşaltılamayan, bantta yapışan ve tipik olarak amaçlanan boşaltmanın dışında bir noktada düşen malzeme olarak tanımlanır ve kaçak malzemelerin ana kaynaklarından biridir. Geri taşımanın tüm konveyör bakım sorunlarının %85’ini oluşturduğu tahmin edilmektedir. Kirli bantlar nedeni ile hareketli bileşenlerde meydana gelen birikim erken aşınmaya neden olabilir. Çalışanları olası işyeri yaralanmalarına ve solunum yolu hastalıklarına maruz bırakan temizlik gereksinimine neden olabilir.
Bir konveyör bandının pratik ve teorik olarak %100 temizlenemeyeceği düşünülebilir. Çünkü bandın yüzeyi ve sıyırıcı uçlar kusursuz değildir. Ancak bu operatörlerin bandı temiz tutmak için proaktif bir yaklaşım benimsememesi gerektiği anlamına gelmez. Çoğu endüstri, en düşük maliyeti sağlamak için etkinlik, bakım kolaylığı ve düşük bant aşınmasının en iyi kombinasyonu olarak yassı kauçuk veya PVC bantlama için metal veya elastomerik uçla temel mekanik kazımaya yönelmiştir.
Bant Sıyırıcılar
Bant sıyırma etkinliği, değişen koşullara ve uygulanan sıyırıcıların sayısı ve türüne ve aldıkları bakıma göre günden güne değişir. Malzemeyi süreçte tutmak, bileşenlerin üzerinde birikmesine ve konveyörün altında birikmesine izin vermekten her zaman daha iyidir. Deneyimler etkili bant temizliği olmadan, dökülme, toz ve geri taşınma nedeniyle toplam yükün %3 kadarının kaybedilebileceğini göstermiştir.
Daha az temizlik gerektiğinde tehlikelere ve yaralanmalara maruz kalma da azalır. Bu da önemli (ancak nadiren düşünülen) dolaylı maliyetlerden tasarruf sağlar. Tutarlı temizleme etkinliğinin anahtarı, bant temizleme sisteminin uygun seçimi, kurulumu, denetimi ve bakımı yoluyla süreci kontrol etmek ve güvenli bir temizleme rutini ve programı oluşturmaktır.
Bir bant üzerinde çoklu mekanik sıyırıcıların kullanılması, uzun süredir etkili bir temizleme yaklaşımı olarak kabul edilmiştir. Çoğu işlemde, elle temizlemeyi haftalık ve hatta aylık görevlerle sınırlarken, geri taşımayı güvenli ve kabul edilebilir bir düzeye indirmek için birden fazla sıyırıcı gerekir.
Etkinlik ve Verimlilik
Ruloların üzerinden geçen yüklü bandın dalgalı hareketi, ince parçacıkların ve nemin kaymasına ve bandın yüzeyinde sıkışmasına neden olma eğilimindedir. Banda yapışan geri taşıma miktarı, metrekare başına birkaç gramdan birkaç kilograma kadar değişebilir. Gerekli bant temizleme seviyesi, banttan temizlenen veya dönüş ruloları tarafından yerinden çıkarılan ve konveyör boşaltma şutunun dışında toplanan geri taşınan malzemenin toplanması / bertaraf edilmesi için yapılan çalışma, planının ve yönteminin bir fonksiyonudur. Bir bant sıyırıcının verimliliğinden bahsederken, başlangıçtaki geri taşıma seviyesini belirtmeden verimlilikten bahsetmek anlamsızdır. İyileştirmenin bir ölçüsü olarak geri dönüşün başlangıç ve bitiş seviyeleri düşünüldüğünde, etkinlik daha iyi bir terimdir. Bunun ile ilgili bazı yönergeler mevcuttur. Bant temizliği için ortalama 100 g/m2 geri taşımanın makul bir performans seviyesi olarak kabul edilmektedir. Ortalama 2 m/s hareket eden ve 7/24 çalışan 1200 mm genişliğinde bir bant, günde yaklaşık 7 tonluk bir temizleme iş yükü yaratacaktır. Bu da bir işçinin hareketli bir konveyöre maruz kalmasını artıran önemli bir işgücü yatırımına ve risk artışlarına neden olur.
Geri taşıma seviyesi temizleme programını belirler. Ancak gerçekte tipik bir bant sıyırıcı etkinliğini aşınma, inceleme ve bakım eksikliği nedeniyle zamanla kaybeder. Ortalama veya yetersiz bakıma sahip sistemlerde, etkinlik değerleri genellikle %40-60 aralığındadır, bu nedenle birden fazla sıyırıcıya ihtiyaç duyulur.
Temizlik Yeri
Ne yazık ki, tasarımcılar, optimum temiz kurulum için yeterli alana odaklanmadan, genellikle tahrik ve gergi tamburlarının etrafındaki yapının en düşük kurulum maliyetine odaklanır. Aşağıdaki şekil, bant sıyırıcıların optimum konumlara montajı için tahliye oluğunda ihtiyaç duyulan temiz alanları göstermektedir. Kurulumlar, uygun inceleme ve bakımı teşvik etmek için çalışma platformunun üzerinde ergonomik bir yükseklikte olmalıdır. Sıyırıcıları optimum konumlara yerleştirmek için tasarım aşamasında dikkatli olunması ve daha etkili denetim, bakım ve bant sıyırıcı performansı sağlayacaktır.
Bant sıyııcılar, bant desteklendiği sürece, bandın dönüş hattı boyunca herhangi bir yere yerleştirilebilir. Banttan temizlenen geri taşınan malzemenin ana malzeme akışına döndürülmesi istendiğinden, çoğu bant sıyırıcı boşaltma şutunun içine kurulur. “Birincil temizleme konumu” olarak tahrik tamburunun temizlenmesi tercih edilir. Bandın kirli tarafının bir durdurma, saptırma tamburu veya dönüş rulolarına ulaşmadan önce temizlenmesi daha az tercih edilir. İkincil konumdaki sıyırıcılar için vibrasyonlu akış şutu gerektirir.
İkincil konum başka bir nedenle karmaşıklaşıyor: geri taşınan malzemenin doğası, dikey yüzeylere yapışabilecek ve eğimli bir şuttan aşağı akmayacak şekildedir. Zor malzemeler veya sulak alanlar üzerinden taşıma gibi kritik uygulamalar için bazen üçüncül bir konum gereklidir. Bu gibi durumlarda, üçüncül sıyırıcılar genellikle bir kutu içine alınır ve atık su bir çökeltme havuzuna yönlendirilir.
Bant Sıyırma Basıncı ve Uç Aşınması
Yeterli temizleme basıncı olmadan, uç bantla temas halinde kalamaz, bu da geri taşınan malzemenin kaldırılmasının zayıf olmasına, uç ve bant aşınmasının artmasına neden olur. Çok fazla sıyırma basıncıyla, elastomerik ucun sapması veya metal uç girintisinin kauçuk banda sürtünmesi nedeniyle temizleme performansı düşer. Aşırı temizleme basıncı ile güç tüketimi de önemli ölçüde artar.
Bir bant sıyırıcının uygun şekilde gergin tutulması, maksimum etkinlik ve en düşük maliyet için kritik öneme sahiptir. Sıyırma basıncı genellikle bakım departmanının dikkatine veya eksikliğine bağlı olarak zamanla değişir. Bazı üreticiler, optimum sıyırma basıncını koruyan ve uçlar aşındığında operatörleri uyaran otomatik gergiler ve aşınma göstergeleri sunmaya başlamıştır.
Son Yorumlar
Birçok bant sıyırma sistemi kurulur ve unutulur. Teknisyenler arasında yapılan bir anket, tüm bantların yaklaşık %25’inde temizleyicilerin takılı olduğunu ve bu yüzdenin yalnızca yaklaşık %25’inin uygun şekilde bakımının yapıldığını göstermiştir. Denetim ve bakım eksikliği, giderek daha düşük bir etkinlik düzeyine, daha yüksek işletme maliyetine ve geri taşınan temizlemeyle ilişkili tehlikelere daha fazla maruz kalmaya neden olur.
Etkili bant temizliği, temizlikçiler için yeterli alan ve ergonomik denetim ve bakım erişimi için iyi konumlandırılmış çalışma platformları ile tasarım aşamasında başlar. Servis dostu tasarımlar üretimi iyileştirir, geri taşımayı en aza indirir ve ekipmanın ömrünü uzatır. Sıyırıcılar optimum konumlara yerleştirilmişse ve erişimi kolaysa, düzenli inceleme, temizlik ve bakımın yapılması ve optimum sonuçların alınması daha olasıdır.